
#C500 CLARK FORKLIFT MANUALS#
Manuals for Service (overhaul / repair) and Operation. Additional technical manuals and service letters for repair and operating.ĬLARK forklift Model: C20/25SU. Additional technical manuals and service letters for repair and operating.ĬLARK forklift Model: C20, 25B, 20BP, CS30. Additional technical manuals and service letters for repair and operating.ĬLARK forklift Model: C, CF, CY and CFY 30-50. Additional technical manuals and service letters for repair and operating.ĬLARK forklift Model: C(Y)60-70-80. Additional technical manuals and service letters for repair and operating.ĬLARK forklift Model: C(Y)500 60/80. With luck I will have you a line card by Saturday so you can examine what you have.CLARK forklift Model: C(Y) 60-70-80. You have run it apparently and if it has not locked up or knocking, it is oiling. That engine runs a very low oil pressure. It holds 5 but no need to waste during trials.Īs for gauges. Change filter, crank and run for 15 min or so, drain, refill with 4 qts of 30 wgt (what it uses) with a new filter. I would drain the oil, put in 3 qts of 30 wgt and 1 of kerosene. It probably has the thermostat that came in it. Those Waukesha engines have to have a good thermostat and be run up to op temp or you will have milky oil in a brand new one. and not knowing what you have going where, be sure to record the wires and positions you remove from the solenoid when removing the starter.įix this starter leak, pressure wash the machine, and use it a little. OEM wiring to the solenoid is fairly tricky. Watch the bolts, one is longer, and if in wrong hole will lock converter up. OEM is plastic, just tap one out of gasket paper using the housing as an anvil. Pull the starter, clean it up and make you a gasket. Didn't trace the middle leak to much it's not near as bad as the starter fluid drip. Atf is dripping down from starter and also towards middle of machine and might be running down to drain plug. Found the dipstick for checking hydraulic fluid. Found ATF 2 gallons for $28, bought a couple, will see how long it lasts. Has me holding off on a restoration though. I think it will be ok no more than we are going to use it. Thinking about taking a cue from previous owner and trying putting some catch pans and oil absorbent rags under machine to keep concrete clean. New guage pegs itself then spikes back and forth quickly. I put an ohm meter on the sender wire and saw a major change from running and not running before I bought a new gauge. Not sure if the sender is not compatible or I received a bad gauge. Tried a new oil pressure gauge today and it didn't work.
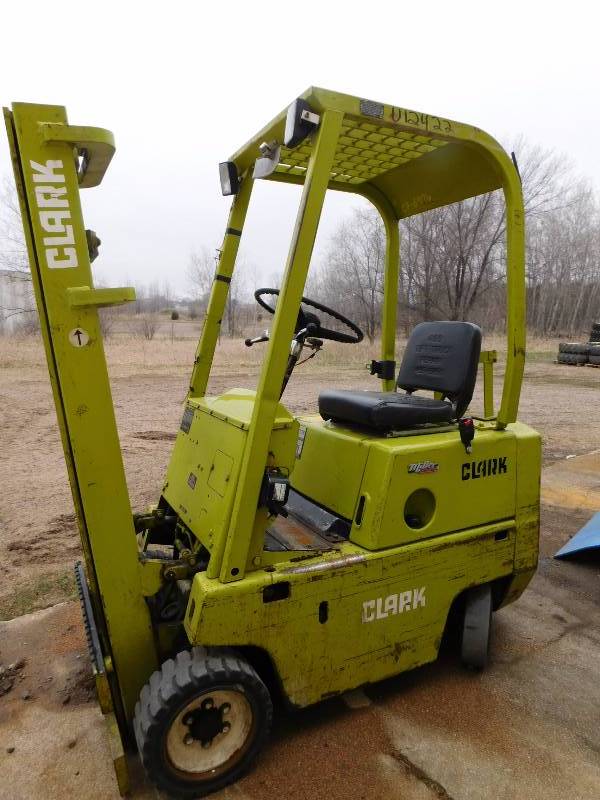
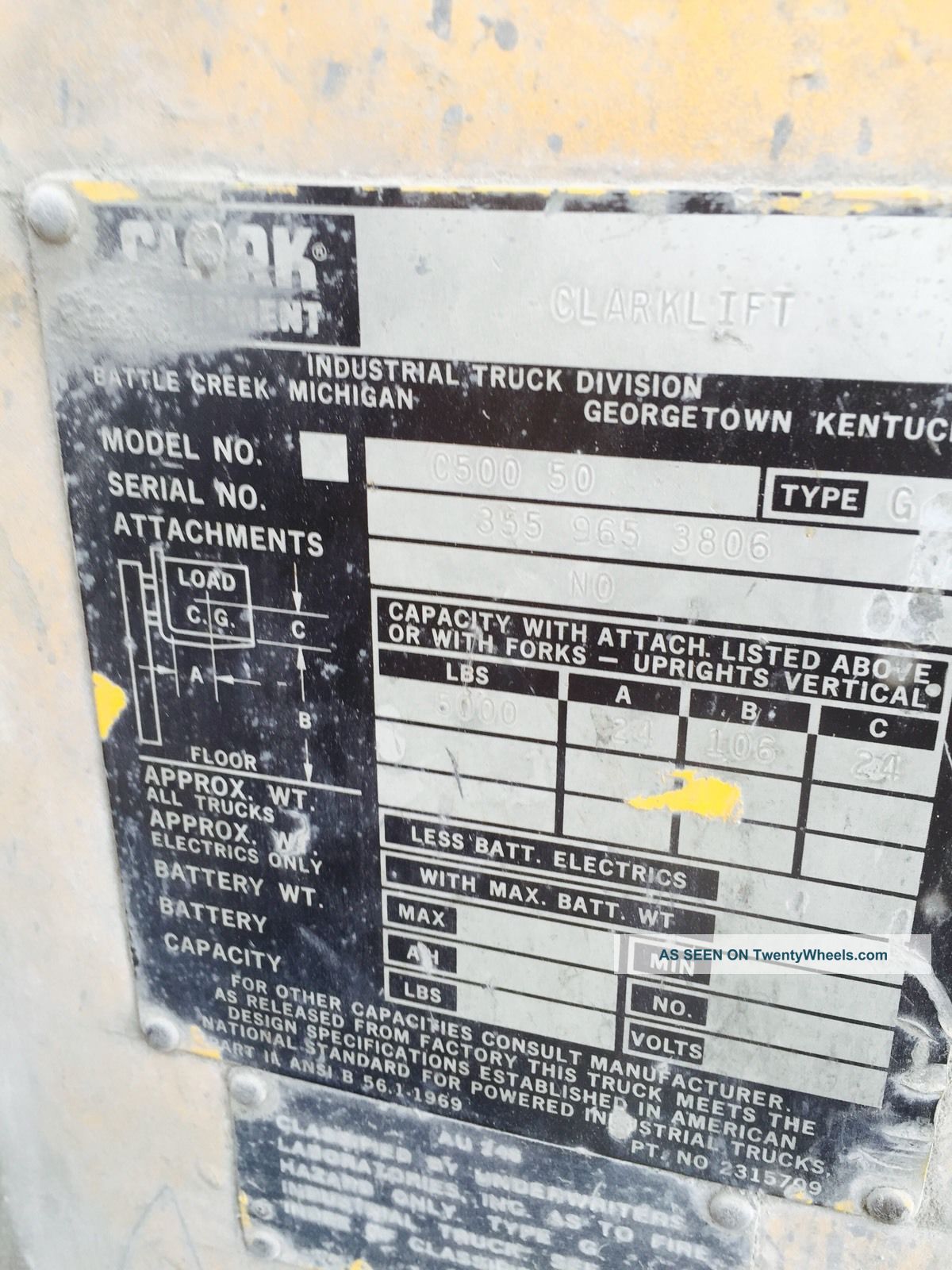
Someone asked about where I was putting tranny fluid in, I'm putting it in front of the mast and checking with engine running. Present one are limited in what we need to see. Suggestion: Re do your same pictures but at a wider angle. (RH side of truck is the Hydraulic oil tank- LH side is the gas tank for gasoline. If empty, will hardly move for a few gallons, then as fills and housing narrows, will rise quickly. Twist left to loosen, pullout, look at dipstick. Where are you putting all this ATF in? Should be area between the (upright to dash) and (between the drive wheels.) A rubber covered plug with a little cross piece to tighten/loosen. Better routing and connections and cheaper.) (Or you get the wiring diagram remove all wiring, and with a few rolls of different colored wire and some spiral loom, rewire the machine properly.
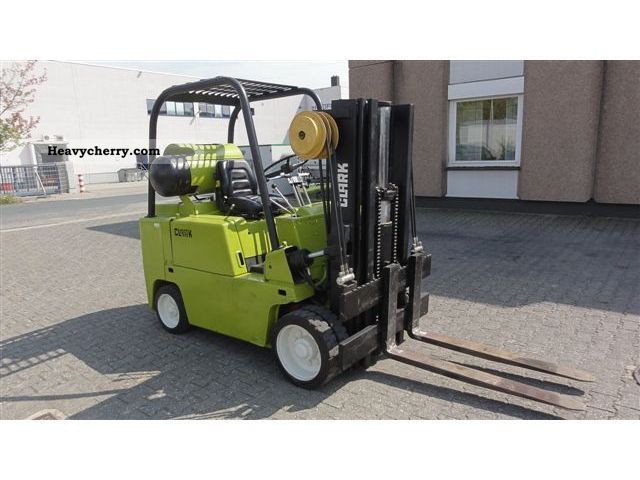

Reason for this cryptic advice is in years of being aware of Clark forklifts, I have never seen the odd extra solenoids appearing on yours. Order a wiring harness for the truck and the wiring diagram. (He can get all these #'s together in his system and order together at once.) ģ.
#C500 CLARK FORKLIFT PLUS#
Plus lots of other numbers you will need. On that card will be the part number for a wiring diagram for that truck, and the wiring harness. Just from the pics you post and the remarks you made regarding fluid leakage:ġ.
